Some information may be outdated.
Local Patrick Betts runs Moab Fixed Hardware
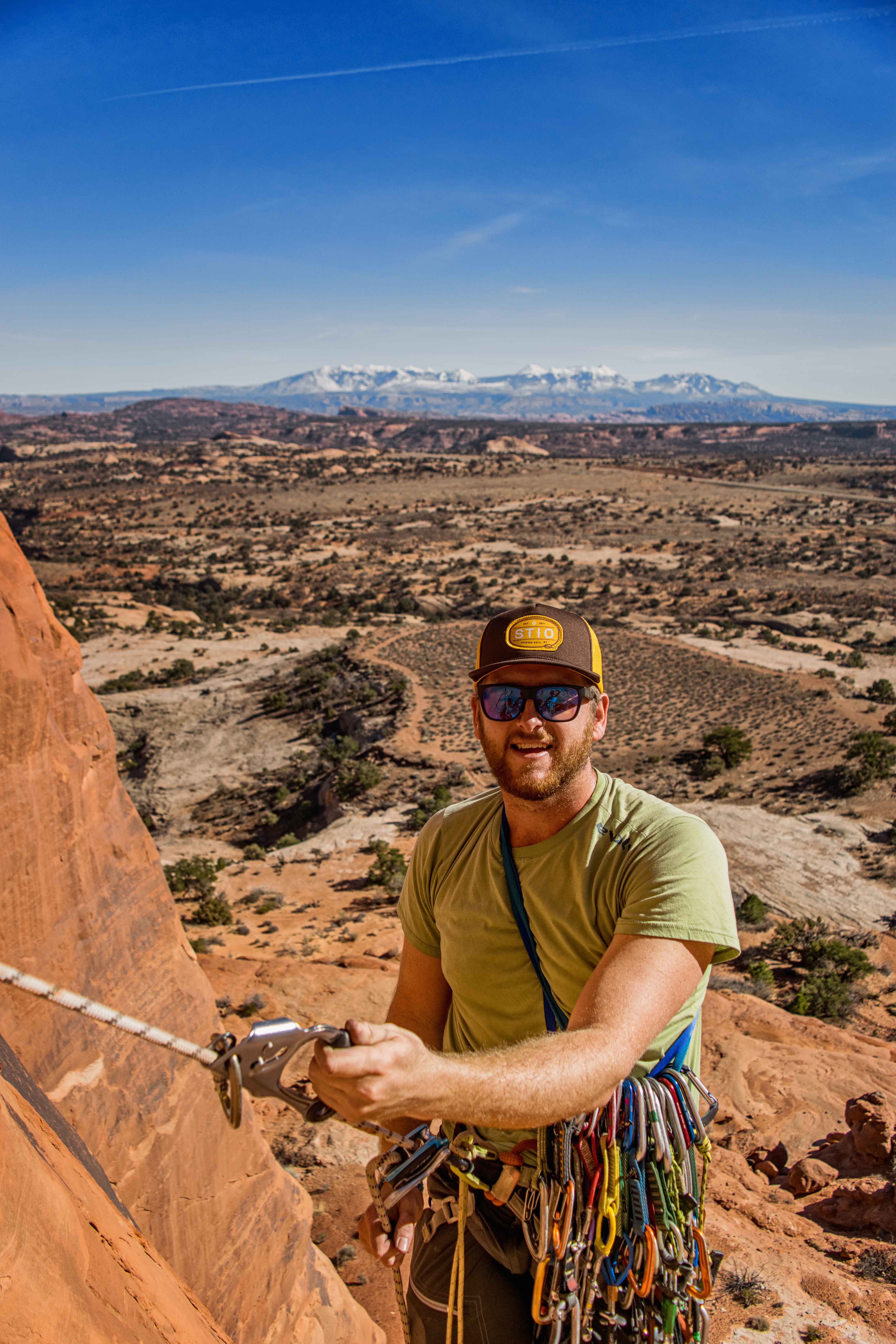
For the last two and a half years, Patrick Betts has been quietly volunteering his time to replace old climbing hardware around Moab with stainless steel glue-in bolts. In October, he officially formed the organization Moab Fixed Hardware, with the continuing goal to upgrade, replace, and modernize bolts and anchors on popular rock climbing routes.
Many routes around Moab still have hardware from the 60s and 70s, which presents a safety issue—in the past, bolts used for climbing protection were only a quarter inch in diameter and made of zinc-plated steel. Modern bolts are usually stainless steel and at least three-eighths inch in diameter.
Through legitimizing Moab Fixed Hardware, Betts hopes to receive more input from the community on where unsafe bolts are, to build a full-time community of climbers who understand how to replace bolts and chains, and to create relationships with various land entities.
Building a Climbing Coalition
“Balancing the impact versus safety is the goal,” Betts said, adding that replacing bolts takes technical skill and an understanding of land regulations and should only be undertaken with proper knowledge.
“I’ve been taking submissions from climbing guides in town who consistently use these routes,” said Betts, who part-time guides at Cliffs and Canyons. Now, individuals can share information on bolts that need replacement by emailing MoabFixedHardware@gmail.com.
To identify suspicious bolts, Access Fund recommends looking for homemade or rusty hangers, and signs of corrosion on the bolts. On the anchor, worn-through links or a chain-washer combo without additional hardware are reportable as a safety issue.
“If I get a list of 30, 40 or 50 route submissions that need attention, I can really grow the number of local people interested in helping,” Betts said, adding that this is key for the organization’s sustainability.
“A lot of climbers in Moab are short-term visitors or are here seasonally, which doesn’t leave a lot of local people interested in maintaining routes through upgrading work,” he said. “I plan to work towards creating an actual climbing coalition that specifically focuses on fixed hardware for climbing routes because it is a pressing matter.”
To become involved in the process of hardware replacement, Betts recommends that everyone carries climbing-specific quick links or chains for the anchors.
“There are lots of anchors that just use webbing; the desert is known for that,” he said. “If just one person can replace that webbing with a chain, then nobody has to put webbing on the anchor again and it’s redundant, equalized, and sustainable.”
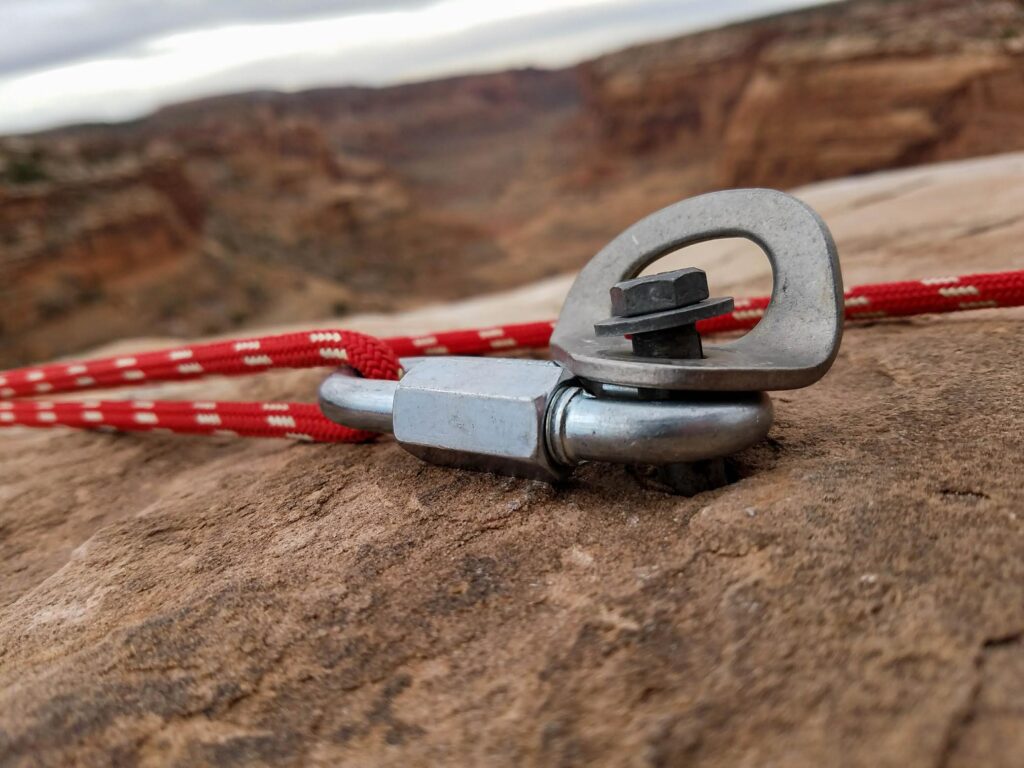
Rebolting with Glue-in Hardware
On sandstone, Betts uses stainless steel glue-in bolts provided by the American Safe Climbing Association (ASCA). The organization’s Lower Off Initiative aims to equip volunteers to rebolt popular cragging areas with modern hardware. The glue-in bolts replace the mechanical bolts used in the past, which have a significantly shorter lifespan in sandstone, Betts said.
“I try to approach rebolting without any intent to drill new holes,” he said. “Most of the time, if you take the time and energy, old bolts should be able to come out. And those holes can be reused for the new bolts with glue.”
Some situations require drilling a new hole; in those cases, the ASCA recommends patching the old hole and camouflaging it to match the rock.
“[Bolts] rust, even if the outside of the bolt might look fine,” Betts said. “It might be totally flush with the rock and not move. But if it’s 25 years old, it’s getting towards the end of its life.”
On Wall Street, a popular climbing area down Potash Road, Betts estimates that he has replaced nearly 30 bolts in the last two months alone. This includes the entirety of the routes ‘Potstash’ and ‘Steel Your Face,’ which are sport climbs on the far left side of the cragging area.
He explained that at Wall Street, many of the routes are low angle or off flat ledges and need extra tending. Rainwater sits on them, which speeds up the erosion process.
“Sometimes the bolts stick out a half inch or three-quarters of an inch. This is not because the bolts were pulled out of the rock, but because the rock has eroded,” Betts said. “There’s really nothing we can do about that after the fact, because it’s geological time erosion.”
Betts anticipates the hardware he’s already replaced will last for another 40 years, but understands that rock falls and erosion are possible with sandstone routes.
Working with Various Land Owners
Climbing areas Wall Street and Ice Cream Parlor are under the jurisdiction of the Bureau of Land Management (BLM), which does not have restrictions for developing climbing routes or installing fixed hardware.
“It’s great because that allows climbers to grow the sport and also upkeep the work as it’s needed,” Betts said. He added that bolt replacements can be more complicated in Wilderness Study Areas, such as Pritchett Canyon, and Arches and Canyonlands national parks.
Depending on the manager, Wilderness Study Areas may require a permit to replace or remove a permanent fixed anchor on climbing routes. Power drills can be used in emergency situations, otherwise only hand drills are allowed.
The National Parks Service does not require a permit to replace existing hardware that is judged to be unsafe. However, they explicitly prohibit the use of power drills, which Betts explained is the best way to drill good holes.
“When I’m faced with a challenge like that…I reach out and tell them I’m rebolting for safety, and I ask if it’s okay,” Betts said. “A lot of times the local offices for these places are usually fine [with rebolting]. Sometimes, they’re not. And so that makes it really tough. And that’s where places see a lot of delay in this work.”
Betts hopes that with Moab Fixed Hardware, a formal relationship can begin to allow for necessary hardware replacement on established climbing routes, encompassing his overarching goal to modernize bolts for safety.
Appreciate the coverage? Help keep local news alive.
Chip in to support the Moab Sun News.